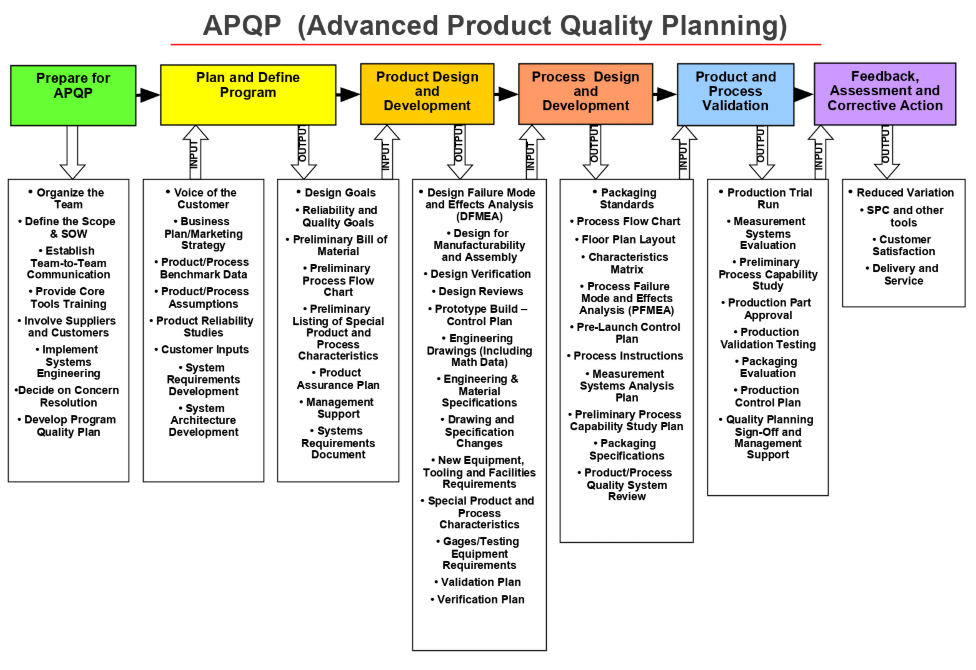
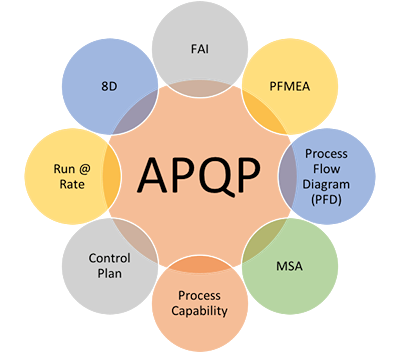
Program Management
• Masterplan preparation
• Dedicated engineering team setup
• PMS usage – Gate Review with customer
• Close work with Customer’s
• Production and manufacturing engineering
• Represent customer in front of OEM and Tier 1
• Detail reporting for monitoring Launch Readiness
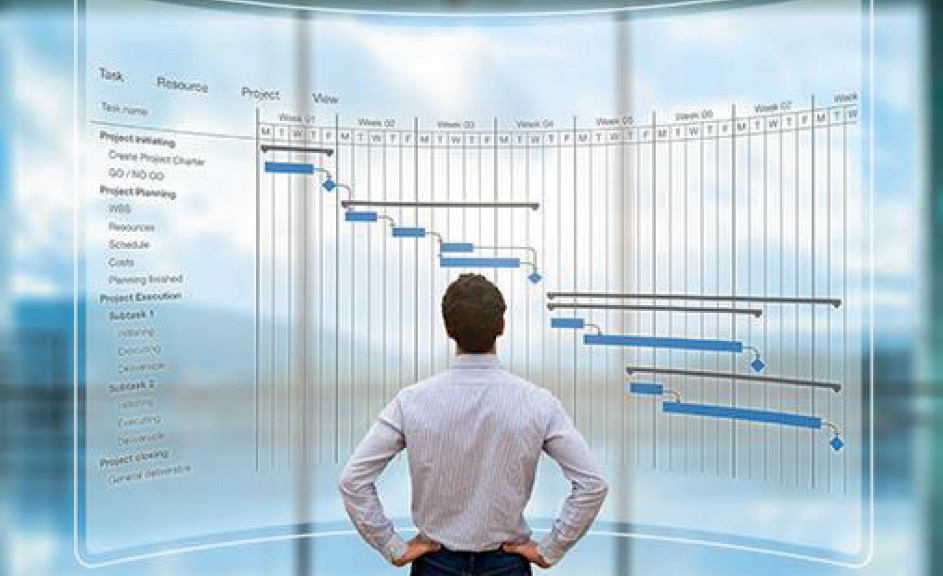

Introduction to Advanced Product Quality Planning (APQP)
Complex products and supply chains present plenty of possibilities for failure,
especially when new products are being launched. Advanced Product Quality
Planning (APQP) is a structured process aimed at ensuring customer satisfaction
with new products or processes.
APQP has existed for decades in many forms and practices. Originally referred to
as Advanced Quality Planning (AQP), APQP is used by progressive companies to
assure quality and performance through planning. Ford Motor Company published
the first Advanced Quality Planning handbook for suppliers in the early 1980’s.
APQP helped Ford suppliers develop appropriate prevention and detection controls
for new products supporting the corporate quality effort. With lessons learned
from Ford AQP, the North American Automotive OEM’s collectively created the APQP
process in 1994 and then later updated in 2008. APQP is intended to aggregate
the common planning activities all automotive OEM’s require into one process.
Suppliers utilize APQP to bring new products and processes to successful
validation and drive continuous improvement.
There are numerous tools and techniques described within APQP. Each tool has
potential value when applied in the correct timing. Tools that have the greatest
impact on product and process success are called the Core Tools. The Core Tools
are expected to be used for compliance to IATF 16949. There are five basic Core
Tools detailed in separate guideline handbooks, including Advanced Product
Quality Planning (APQP). The other Core Tools are:
Failure Mode and Effects Analysis (FMEA)
Measurement Systems Analysis (MSA)
Statistical Process Control (SPC)
Production Part Approval Process (PPAP)
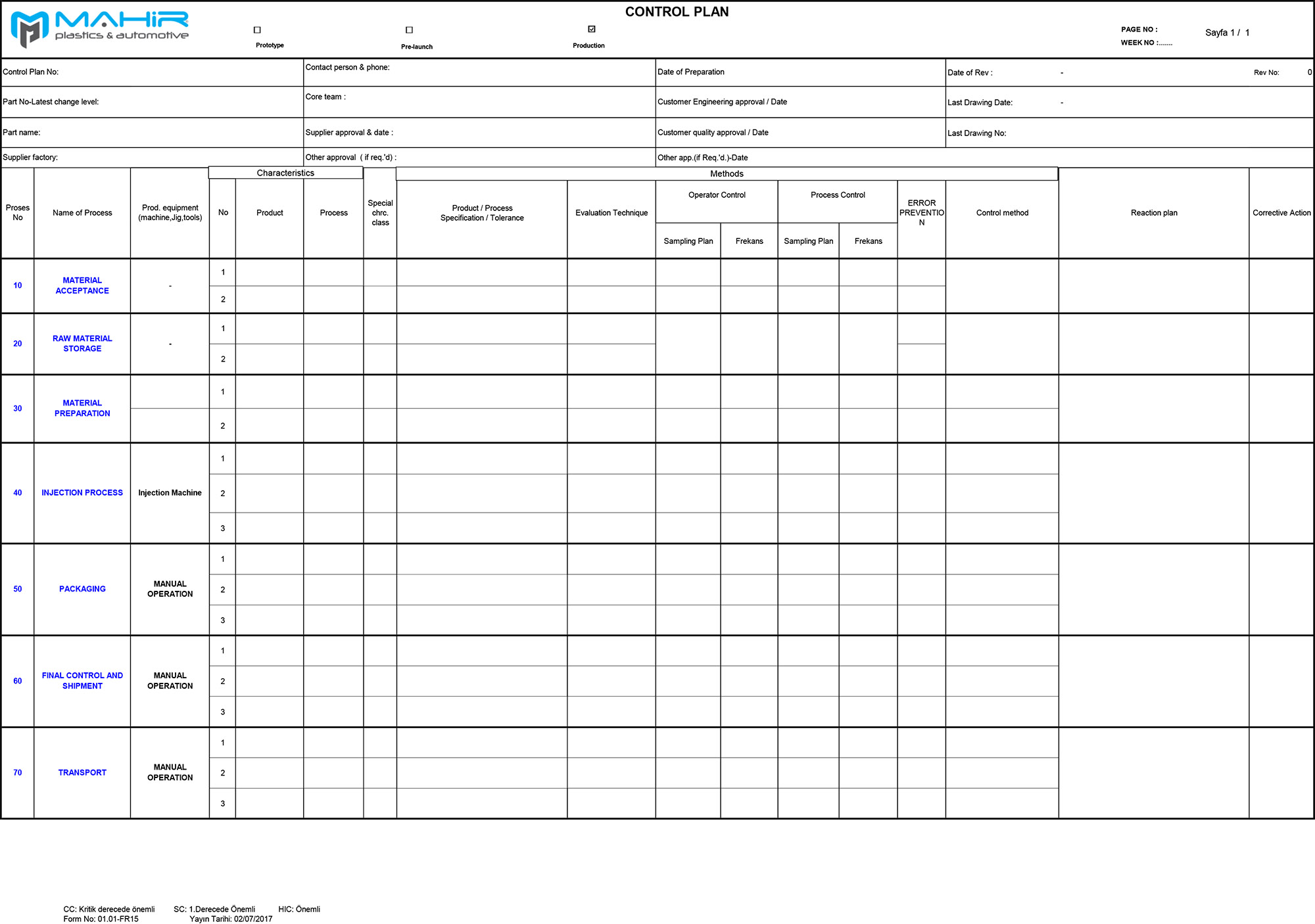